Log in
Search
Latest topics
» Purchased the last of any bult engines from Ken Enyaby getback Today at 7:24 am
» My N-1R build log
by rsv1cox Today at 7:05 am
» Funny what you find when you go looking
by rsv1cox Yesterday at 3:21 pm
» Landing-gear tips
by 1975 control line guy Yesterday at 8:17 am
» Cox NaBOO - Just in time for Halloween
by rsv1cox Tue Nov 19, 2024 6:35 pm
» Canada Post strike - We are still shipping :)
by Cox International Tue Nov 19, 2024 12:01 pm
» Duende V model from RC Model magazine 1983.
by getback Tue Nov 19, 2024 6:08 am
» My current avatar photo
by roddie Mon Nov 18, 2024 9:05 pm
» My latest doodle...
by TD ABUSER Mon Nov 18, 2024 11:30 am
» Brushless motors?
by rsv1cox Sun Nov 17, 2024 6:40 pm
» Free Flight Radio Assist
by rdw777 Sun Nov 17, 2024 6:03 pm
» Tribute Shoestring build
by amurphy6812 Sun Nov 17, 2024 5:43 pm
Cox Engine of The Month
some thoughts for bernie
Page 2 of 2
Page 2 of 2 • 1, 2
Re: some thoughts for bernie
A CNC machine can do micro size operations beyond the
human eye. Material by the pound could make a lot of engines
I show a scale pic of the TD .010 compared to what a
TD .0020 rendering would appear visually full size.
Enough power to make around 8w of energy perhaps
1.2oz of thrust with 30% nitro. Good for a 3oz
2 or 3ch micro back yard flyer.

human eye. Material by the pound could make a lot of engines
I show a scale pic of the TD .010 compared to what a
TD .0020 rendering would appear visually full size.
Enough power to make around 8w of energy perhaps
1.2oz of thrust with 30% nitro. Good for a 3oz
2 or 3ch micro back yard flyer.


1/2A Nut- Top Poster
- Posts : 3536
Join date : 2013-10-20
Age : 61
Location : Brad in Texas
Re: some thoughts for bernie
And the real proportion:

BTW the Roaring 20 my 010 flew weighs around 8 oz, so the 010 is a real muscleful lil bastard
https://www.coxengineforum.com/gallery/Personal-album-of-balogh/2011-11-19-1936341-pic_328.htm

BTW the Roaring 20 my 010 flew weighs around 8 oz, so the 010 is a real muscleful lil bastard
https://www.coxengineforum.com/gallery/Personal-album-of-balogh/2011-11-19-1936341-pic_328.htm
Last edited by balogh on Sun Jan 31, 2016 3:24 am; edited 2 times in total
balogh- Top Poster
Posts : 4958
Join date : 2011-11-06
Age : 66
Location : Budapest Hungary
Re: some thoughts for bernie
so how much would all the machinery cost to make an 010 and 020's?
cox24711- Platinum Member
- Posts : 722
Join date : 2014-01-18
Age : 21
Location : Noosa Queensland Australia
Re: some thoughts for bernie
cox24711 wrote:so how much would all the machinery cost to make an 010 and 020's?
More that your lunch money added to my lunch money.
If I had a quarter million US dollar budget and were to buy machines... I don't know if I would have enough. A multi-axis mill is not capable of holding the tolerances for the cylinder bore and piston sides, but will hold superb tolerances for everything else and can allow for indexing the cylinders as a bonus - not as an added step.
Wire EDM might be the way to go for making small batches of cylinder bores as it produces a ground-like finish and is capable of the +- .0002 inch tolerances. This can also finish the outside of the piston. The inside of the piston and outside of the cylinder would be better finished on the mill/lathe prior to EDM. I understand EDM can also cut the ports in at the same time.
So 2 machines... each with a starting price tag of around $100k
The small bonus here is these two machines exist, together, in a large number of shops worldwide, so finding a shop to do this might be possible. The specialized tooling is at least limited. Holding fixtures would be needed but those would be made in-house.
The hand labor of switching parts might actually be the limiting cost in a production run of pistons/cylinders. I know little about EDM specifics like process speed and such. I have seen the results of it though.
Sourcing extrusion (pultrusion) that is already brass/bronze inside the aluminum will probably cost less than having the bushing installed after the fact. Using the same anodized aluminum bushing that was used originally is of course much less expensive.
The original engines were made on manual turret lathes, the staple of all production for over 50 years. Tooling was made to match each and every cut and process so that tolerances could be held extra tight, and production speed could be increased. This meant that every bit of tooling was custom. It also meant that a relatively inexpensive machine could do some truly great work.
Lastly in order to get super high tolerances out of any machine a proper foundation will be needed. The foundation will need to be massive and vibration isolated so people walking, and traffic outside does not mess up the cut.
These engines would not pay for the machines to make them, Even if you were to produce a full line of all engine sizes I think there would be a struggle. This shop would have to be producing many different parts for many different customers to stay in business.
Phil
pkrankow- Top Poster
- Posts : 3025
Join date : 2012-10-02
Location : Ohio
Re: some thoughts for bernie
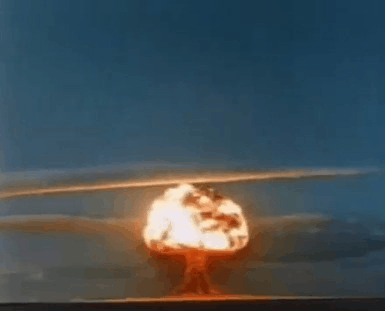
_________________
Don't Panic!
...and never Ever think about how good you are at something...
while you're doing it!
My Hot Rock & Blues Playlist
...and never Ever think about how good you are at something...
while you're doing it!
My Hot Rock & Blues Playlist
RknRusty- Rest In Peace
- Posts : 10869
Join date : 2011-08-10
Age : 68
Location : South Carolina, USA
Re: some thoughts for bernie
Rusty, I couldn't of said it better.
Ken Cook- Top Poster
- Posts : 5635
Join date : 2012-03-27
Location : pennsylvania
Re: some thoughts for bernie
You can farm out the work for the cylinder cutting to a shop already setup.
A local steel machining company retained my engineering firm to design a foundation stable enough
to laser cut parts without any deviation in lieu of a active train track within 80 yrds. of the bldg.
Our solution used 4 concrete steel reinforced 18" dia. piers around 24ft depth drilled down min.
12" into bedrock. Pier caps with an isolated top slab from existing sub grade was used.
The 10" thick steel reinforced top slab was 20' x 20' enough space to park 2 cutting tables.
Small compact CNC machines are cheap these days here is an example
Able to do some of the more simple tasks.
Othermill - Compact Precision CNC + PCB Milling Machine
PRODUCT ID: 2323
$2,199.00

Does not come with a PC but CNC--for under $2000
Gretchen is on standby ready to feed and tend to the machine for 16.95 per hr.
An operator could set up and hit the go button on multiple machines per hr.
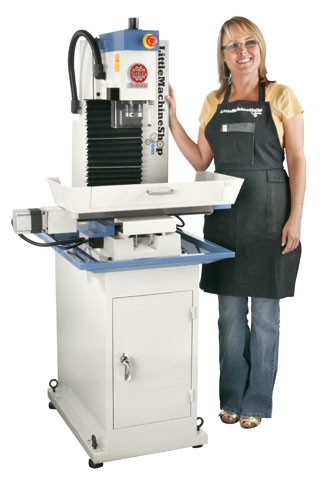
A local steel machining company retained my engineering firm to design a foundation stable enough
to laser cut parts without any deviation in lieu of a active train track within 80 yrds. of the bldg.
Our solution used 4 concrete steel reinforced 18" dia. piers around 24ft depth drilled down min.
12" into bedrock. Pier caps with an isolated top slab from existing sub grade was used.
The 10" thick steel reinforced top slab was 20' x 20' enough space to park 2 cutting tables.
Small compact CNC machines are cheap these days here is an example
Able to do some of the more simple tasks.
Othermill - Compact Precision CNC + PCB Milling Machine
PRODUCT ID: 2323
$2,199.00

Does not come with a PC but CNC--for under $2000
Gretchen is on standby ready to feed and tend to the machine for 16.95 per hr.
An operator could set up and hit the go button on multiple machines per hr.
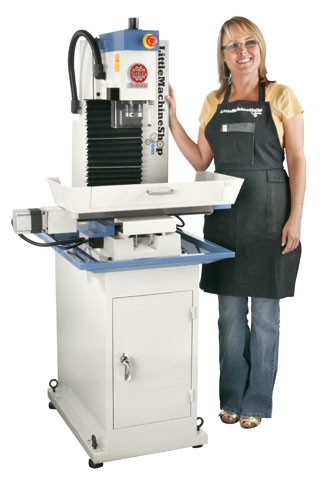
1/2A Nut- Top Poster
- Posts : 3536
Join date : 2013-10-20
Age : 61
Location : Brad in Texas
Re: some thoughts for bernie
Originally Cox engines sold in millions, you would be extremely fortunate now to reach hundreds. The recent demise of the tiny engine producer CS Engines demonstrates this quite well.
They made engines in small batches aimed mainly at collectors. Never more than 100 of anything.
This for example is the CS Navo 0.37cc special - only 22 produced


They had trouble shifting all their production batches.
You also have to remember that IC engines have been overshadowed by ready to fly electrickery jobbies and very few now build model aircraft.
I am not convinced that production accuracy was as good as often described. I think the accuracy came as a consequence of mass production and quality control.
Because of the volume of parts produced they could be matched for fits and Cox engines took this seriously.
This site shows "some" of the machinery used to produce the engines
http://www.mh-aerotools.de/airfoils/cox_album.htm
If you scroll down to this picture

You will see the following text
The piece of equipment in front of Roy Cox was used to check the seal and tolerances of the piston and cylinder.
Pistons were matched by hand into each cylinder and the women were quite adept at judging the proper "feel" of this fit. However, just because it felt right was no guarantee that the piston was truly round. In fact it may be out of round or "clover leafed." So, although it may appear to fit, the piston could still leak compression.
Thus, with this air gauge equipment, which was designed and built in house, pistons were held inside the cylinder and compressed air was then forced into the firing chamber. The piston's ability to maintain the air pressure, as viewed by the air gauge, was the assurance of a proper match. The gauges carried indicators which defined the limits of a acceptable cylinder piston fit.
The labour market has also changed. It is unlikely that anything like this could be recreated in the United States again and would be hived off to the far east where quality control can be a little lacking.
They made engines in small batches aimed mainly at collectors. Never more than 100 of anything.
This for example is the CS Navo 0.37cc special - only 22 produced


They had trouble shifting all their production batches.
You also have to remember that IC engines have been overshadowed by ready to fly electrickery jobbies and very few now build model aircraft.
I am not convinced that production accuracy was as good as often described. I think the accuracy came as a consequence of mass production and quality control.
Because of the volume of parts produced they could be matched for fits and Cox engines took this seriously.
This site shows "some" of the machinery used to produce the engines
http://www.mh-aerotools.de/airfoils/cox_album.htm
If you scroll down to this picture

You will see the following text
The piece of equipment in front of Roy Cox was used to check the seal and tolerances of the piston and cylinder.
Pistons were matched by hand into each cylinder and the women were quite adept at judging the proper "feel" of this fit. However, just because it felt right was no guarantee that the piston was truly round. In fact it may be out of round or "clover leafed." So, although it may appear to fit, the piston could still leak compression.
Thus, with this air gauge equipment, which was designed and built in house, pistons were held inside the cylinder and compressed air was then forced into the firing chamber. The piston's ability to maintain the air pressure, as viewed by the air gauge, was the assurance of a proper match. The gauges carried indicators which defined the limits of a acceptable cylinder piston fit.
The labour market has also changed. It is unlikely that anything like this could be recreated in the United States again and would be hived off to the far east where quality control can be a little lacking.
ian1954- Diamond Member
- Posts : 2688
Join date : 2011-11-16
Age : 70
Location : England
Re: some thoughts for bernie
ian1954 wrote:far east where quality control can be a little lacking.




I think this man is doing rather well!!!



OVERLORD- Diamond Member
- Posts : 1807
Join date : 2013-03-19
Age : 58
Location : Normandy, France
Re: some thoughts for bernie
akjgardner wrote:3D Printing technology is to the point to where you could probably print you one. Don't know how the metallurgy would be on it. Im sure it would have to be heat treated, Just thinking out loud
Jason and Ian are two CEF members that have 3D printers. Although the machines currently use plastic to make a part, I feel that it's only a matter of time before they're developed to use metals. The future of machining.. will be the addition of material rather than the removal. Even with using plastic as a media.. re-making a mold to re-produce an extinct part is possible.. and a much less costly process.
Sure it's unlikely that tiny-displacement engines will ever be mass-produced again.. but that doesn't stop some people having a passion for them.. to build their own. Greg, is there an industrial-arts program at your school? That would be a great thing for you to explore. I took mechanical-drawing back in high-school.. and find now; that it's very helpful when I draw my own model plans. I wish I had taken more industrial engineering classes back then.. but I didn't. With today's technology.. you'd be exposed to the latest designing and machining tools. A precision-machinist/tool-maker will always be in demand. Even if you don't choose it as a career-path.. it's knowledge that will serve you well if you're interested in what makes things "tick". In the meanwhile.. keep running/acquiring model engines. There's still plenty of them out there!
Re: some thoughts for bernie
A lot of gun makers are using an injection molding process called MIM for small parts, judging buy the griping going on they don't hold up well.
https://en.wikipedia.org/wiki/Metal_injection_molding
https://en.wikipedia.org/wiki/Metal_injection_molding
crankbndr- Top Poster
- Posts : 3109
Join date : 2011-12-10
Location : Homestead FL
Re: some thoughts for bernie
I think with today's CNC machinery it would be (relatively) easy to create an exact and functional copy of Tee Dee .010 or any other engine that has practically no cast metal parts. Of course cast part lookalikes could also be modeled and milled but it would be a lot more difficult.
It would be expensive to create the tooling required to do the aluminium extrusion, but in a small scale production it would be no problem to make the crankcase out of solid billet. Piston would be a challenge I think, with the copper coating, ball joint and such, but it would still be "doable". There are also new methods such as nano-coatings to reduce friction and wear, these could be utilized in all the internals of a repro engine.
For plastics, there's a method called SLS, Selective Laser Sintering. I've seen some nylon parts made using this method and it is far superior to the more common method as far as the strength and surface quality are concerned. This might actually be something worth investigating for manufacturing of low volume plastic parts such as throttle bodies for Big Medallions and Tee Dees.
So, if there were a will there would be a way. But for the cost to set up a manufacturing system required, one could probably buy all the available NIB Tee Dees in the world
It would be expensive to create the tooling required to do the aluminium extrusion, but in a small scale production it would be no problem to make the crankcase out of solid billet. Piston would be a challenge I think, with the copper coating, ball joint and such, but it would still be "doable". There are also new methods such as nano-coatings to reduce friction and wear, these could be utilized in all the internals of a repro engine.
For plastics, there's a method called SLS, Selective Laser Sintering. I've seen some nylon parts made using this method and it is far superior to the more common method as far as the strength and surface quality are concerned. This might actually be something worth investigating for manufacturing of low volume plastic parts such as throttle bodies for Big Medallions and Tee Dees.
So, if there were a will there would be a way. But for the cost to set up a manufacturing system required, one could probably buy all the available NIB Tee Dees in the world

KariFS- Diamond Member
- Posts : 2044
Join date : 2014-10-10
Age : 53
Re: some thoughts for bernie
ian1954 wrote:...............
This site shows "some" of the machinery used to produce the engines
http://www.mh-aerotools.de/airfoils/cox_album.htm
If you scroll down to this picture
.
I am not sure who feels what when seeing these old photos with the bonanza of engine parts and planes. I would like to go back in time to the late 50's and early 60's and get an employment as a machine operator right in the heart of the engine shop...
balogh- Top Poster
Posts : 4958
Join date : 2011-11-06
Age : 66
Location : Budapest Hungary
Page 2 of 2 • 1, 2

» HUGE lot of Cox items for sale!
» Another proposed design by Roddie
» Me and the Bean (progress!)
» COX TeeDee 05 for sale mint cond.
» Drone registration
» Another proposed design by Roddie
» Me and the Bean (progress!)
» COX TeeDee 05 for sale mint cond.
» Drone registration
Page 2 of 2
Permissions in this forum:
You cannot reply to topics in this forum