Log in
Search
Latest topics
» Tee Dee .020 combat modelby roddie Today at 1:34 pm
» Chocolate chip cookie dough.........
by roddie Today at 1:13 pm
» Purchased the last of any bult engines from Ken Enya
by sosam117 Today at 11:32 am
» Free Flight Radio Assist
by rdw777 Today at 9:24 am
» My latest doodle...
by batjac Yesterday at 9:47 pm
» My N-1R build log
by roddie Yesterday at 8:50 pm
» Funny what you find when you go looking
by rsv1cox Wed Nov 20, 2024 3:21 pm
» Landing-gear tips
by 1975 control line guy Wed Nov 20, 2024 8:17 am
» Cox NaBOO - Just in time for Halloween
by rsv1cox Tue Nov 19, 2024 6:35 pm
» Canada Post strike - We are still shipping :)
by Cox International Tue Nov 19, 2024 12:01 pm
» Duende V model from RC Model magazine 1983.
by getback Tue Nov 19, 2024 6:08 am
» My current avatar photo
by roddie Mon Nov 18, 2024 9:05 pm
Cox Engine of The Month
Reed clearance/gap
Page 1 of 1
Reed clearance/gap
I searched the threads here; including Paul G's Mouse Racing tips, and couldn't find any definitive info. on the reed's clearance. I feel that there's more to be examined with the way the reed operates.. that will make or break good performance.
As we know; there are several reed materials and thicknesses in use.. as well as shapes.
Materials: (most commonly found) Beryllium/Copper, Mylar, Stainless Steel and Teflon.
Thickness: I assume that the differing thicknesses between the material types is directly related to their degree of "flex".. or they would not differ in thickness. (your thoughts?)
Beryllium/Copper=.001" (.025mm)
Stainless Steel=.002" (.050mm)
Mylar*=.005" (.125mm) *both star and rectangular shape versions.
Teflon=.010" (.25mm)
Shape: Cross/star or later rectangular, would not seem to matter; as long as the reed's cross section is supported by it's retainer system.. whether it be a spring-steel circlip.. or the later plastic "cap" style retainer. I have only seen the Beryllium/Copper reed in a cross/star shape. I have Mylar reeds in both shapes.. and they are the same thickness. (your thoughts?)
Function: Here's where some discussion will surely ensue (I'm hoping)... The basic function of the reed is to open and close (valve) with each engine stroke, allowing a metered amount of fuel/air into the crankcase for combustion. Like any valve.. it must seal when it closes. At 15,000 rpm.. the open/close cycle happens 250 times/second!
Given the differing thicknesses and degree of flex between the various reeds; their retention system must come into play. Paul Gibeault states that the Mylar reed is necessary for performance and that the star/cross Beryllium/Copper reed will begin to "float" at an rpm far below optimal for a performance engine. I would suspect the main reason to be because of the Copper reed's thickness. The circlip-style retainer that was originally designed for it by Cox, allows the thin reed to rotate freely in it's housing without pinching it at it's OD. The thicker (x5) Mylar cross/star reed is said to provide better performance. Some say that the Mylar type should also rotate freely in the housing while being retained by the circlip. If it will rotate freely without any modification.. this would indicate a clearance of at least .005" under the circlip. Is this why the thinner Copper reed floats at high rpm's? Is it's rigidity (or lack there of..) a factor? (your thoughts?)
Flex: When the reed opens, it must be retained from flexing too far away from the seat. Circlips can be.. and have been mistakenly installed backwards, preventing the reed from opening at all.. but when installed correctly; what is the optimum "gap" for the reed to open? Should this gap be checked/adjusted? It's obviously "pre-set" and non-adjustable on the newer plastic style retainers. I checked two random circlips and found a significant difference in the center gap. Perhaps this difference would only show-up in a slightly different needle-setting? Could less of a gap prevent a Copper Reed from floating at high rpm's? Would more of a gap with "any" reed allow more mixture into the crankcase up to a point where reed-float occurs? (your thoughts?)
I would ascertain the "star-shape" to be a better/smoother flowing reed.. (as opposed to the rectangular shape) in any type of housing/holder, having it's 4 symmetrically-radiussed tabs. This reed pulls away from the seat with 360 degrees of suspension-support.. and the mixture passes through/over 4 symmetrical edges which in my opinion; makes for a much smoother flow. The rectangular shape reed by comparison, has two sharp-flat edges for the fuel mixture to flow past.. as well as only being retained on two sides.. 180 degrees apart. (your thoughts?)
A closing question: Could the thin Beryllium/Copper (star) reed be hard-anodized to improve it's performance? Paul G. states that using a Stainless Steel reed will eventually wear the anodizing off of an integral (metal) tanks' venturi mouth. Perhaps this would be a consideration in anodizing a Copper reed? Perhaps anodizing would render the Copper reed too brittle?
As we know; there are several reed materials and thicknesses in use.. as well as shapes.
Materials: (most commonly found) Beryllium/Copper, Mylar, Stainless Steel and Teflon.
Thickness: I assume that the differing thicknesses between the material types is directly related to their degree of "flex".. or they would not differ in thickness. (your thoughts?)
Beryllium/Copper=.001" (.025mm)
Stainless Steel=.002" (.050mm)
Mylar*=.005" (.125mm) *both star and rectangular shape versions.
Teflon=.010" (.25mm)
Shape: Cross/star or later rectangular, would not seem to matter; as long as the reed's cross section is supported by it's retainer system.. whether it be a spring-steel circlip.. or the later plastic "cap" style retainer. I have only seen the Beryllium/Copper reed in a cross/star shape. I have Mylar reeds in both shapes.. and they are the same thickness. (your thoughts?)
Function: Here's where some discussion will surely ensue (I'm hoping)... The basic function of the reed is to open and close (valve) with each engine stroke, allowing a metered amount of fuel/air into the crankcase for combustion. Like any valve.. it must seal when it closes. At 15,000 rpm.. the open/close cycle happens 250 times/second!
Given the differing thicknesses and degree of flex between the various reeds; their retention system must come into play. Paul Gibeault states that the Mylar reed is necessary for performance and that the star/cross Beryllium/Copper reed will begin to "float" at an rpm far below optimal for a performance engine. I would suspect the main reason to be because of the Copper reed's thickness. The circlip-style retainer that was originally designed for it by Cox, allows the thin reed to rotate freely in it's housing without pinching it at it's OD. The thicker (x5) Mylar cross/star reed is said to provide better performance. Some say that the Mylar type should also rotate freely in the housing while being retained by the circlip. If it will rotate freely without any modification.. this would indicate a clearance of at least .005" under the circlip. Is this why the thinner Copper reed floats at high rpm's? Is it's rigidity (or lack there of..) a factor? (your thoughts?)
Flex: When the reed opens, it must be retained from flexing too far away from the seat. Circlips can be.. and have been mistakenly installed backwards, preventing the reed from opening at all.. but when installed correctly; what is the optimum "gap" for the reed to open? Should this gap be checked/adjusted? It's obviously "pre-set" and non-adjustable on the newer plastic style retainers. I checked two random circlips and found a significant difference in the center gap. Perhaps this difference would only show-up in a slightly different needle-setting? Could less of a gap prevent a Copper Reed from floating at high rpm's? Would more of a gap with "any" reed allow more mixture into the crankcase up to a point where reed-float occurs? (your thoughts?)
I would ascertain the "star-shape" to be a better/smoother flowing reed.. (as opposed to the rectangular shape) in any type of housing/holder, having it's 4 symmetrically-radiussed tabs. This reed pulls away from the seat with 360 degrees of suspension-support.. and the mixture passes through/over 4 symmetrical edges which in my opinion; makes for a much smoother flow. The rectangular shape reed by comparison, has two sharp-flat edges for the fuel mixture to flow past.. as well as only being retained on two sides.. 180 degrees apart. (your thoughts?)
A closing question: Could the thin Beryllium/Copper (star) reed be hard-anodized to improve it's performance? Paul G. states that using a Stainless Steel reed will eventually wear the anodizing off of an integral (metal) tanks' venturi mouth. Perhaps this would be a consideration in anodizing a Copper reed? Perhaps anodizing would render the Copper reed too brittle?
Re: Reed clearance/gap
I have in the past put the circlip on a stone and put a flat area on the side facing the reed, can't remember why, must have been to free it up a bit.
crankbndr- Top Poster
- Posts : 3109
Join date : 2011-12-10
Location : Homestead FL
Re: Reed clearance/gap
Much like Doug, I too file my clips flat to allow the reeds to rotate.
I think the plastic reed retainer is the way to go for speed events. I did use a clip in the Babe Bee for the tach race a couple years back. It took some working to allow the stainless reed to rotate, but it paid off.
I think the plastic reed retainer is the way to go for speed events. I did use a clip in the Babe Bee for the tach race a couple years back. It took some working to allow the stainless reed to rotate, but it paid off.
Cribbs74- Moderator
Posts : 11907
Join date : 2011-10-24
Age : 50
Location : Tuttle, OK
Re: Reed clearance/gap
I realize that my OP was a lot to digest.. (you know me...
) Being a reedie fan, I'm just curious and intrigued about this part of the engine. I've read so much about hop-ups and performance tweaks.. but it seems like the reed is for the most part thought of as; "if it works.. then it's fine".
I forgot to mention "Crystal" as another reed type that I've seen. I assume it's Polycarbonate.. but I don't know the thickness that's used.
It's the varying thicknesses between the different materials that's interesting to me. It would seem that a retainer system would need to be matched to varying reed thicknesses in order to function optimally.
Doug and Ron; Both of you state that you've altered your spring-steel circlip retainers for a less binding reed fit.. which is one way to accomplish this.
Rather than thinning-out a circlip.. I wonder if the reed itself could be thinned by placing it between two small sanding blocks faced with 600 grit (or finer) paper.. and alternately twisting the blocks.. rather than using a linear sanding motion? Maybe .0005" would be enough of a reduction in thickness. For example; a .005" Mylar reed may only need to be thinned to .0045" to achieve the desired fit. A good vernier-caliper could be used to check the thickness during the thinning process. It's worth trying.. and might be better to sacrifice a reed rather than to alter a circlip.

I forgot to mention "Crystal" as another reed type that I've seen. I assume it's Polycarbonate.. but I don't know the thickness that's used.
It's the varying thicknesses between the different materials that's interesting to me. It would seem that a retainer system would need to be matched to varying reed thicknesses in order to function optimally.
Doug and Ron; Both of you state that you've altered your spring-steel circlip retainers for a less binding reed fit.. which is one way to accomplish this.
Rather than thinning-out a circlip.. I wonder if the reed itself could be thinned by placing it between two small sanding blocks faced with 600 grit (or finer) paper.. and alternately twisting the blocks.. rather than using a linear sanding motion? Maybe .0005" would be enough of a reduction in thickness. For example; a .005" Mylar reed may only need to be thinned to .0045" to achieve the desired fit. A good vernier-caliper could be used to check the thickness during the thinning process. It's worth trying.. and might be better to sacrifice a reed rather than to alter a circlip.
Re: Reed clearance/gap
Interesting discussion here.
Regarding reed clearance, I noticed a while ago, a difference
in g-clip wire size.
In my fuzzy photo, you'll see an older cox clip on the left, and
one of Bernie's newer ones on the right.
The wire used on the older one measures .0275", and Bernie's
measures .0320" . Bernie's can be identified by the flat spot on
circumfrence, as pictured upper right.
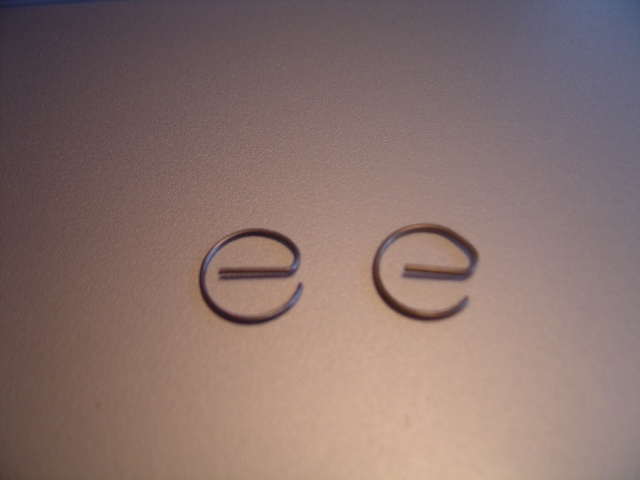
Maybe this will alleviate some confusion, or add to it(hope not).
Also, the "crystal" reed measures .0040.
Bob
Regarding reed clearance, I noticed a while ago, a difference
in g-clip wire size.
In my fuzzy photo, you'll see an older cox clip on the left, and
one of Bernie's newer ones on the right.
The wire used on the older one measures .0275", and Bernie's
measures .0320" . Bernie's can be identified by the flat spot on
circumfrence, as pictured upper right.
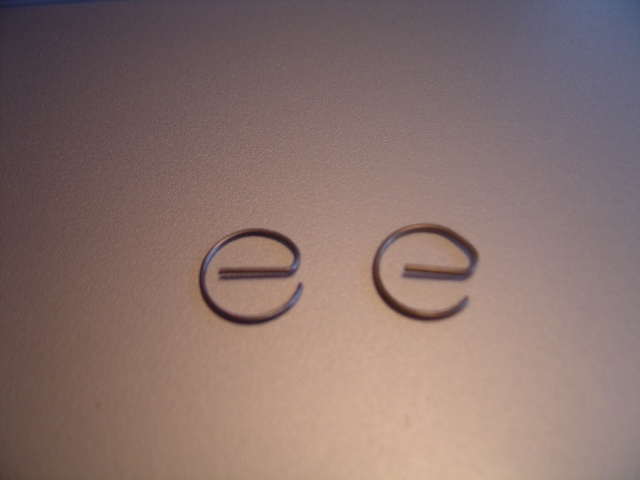
Maybe this will alleviate some confusion, or add to it(hope not).
Also, the "crystal" reed measures .0040.
Bob
dckrsn- Diamond Member
- Posts : 2750
Join date : 2010-10-21
Age : 71
Location : Long Island, New York
Re: Reed clearance/gap
Bob exposes another interesting factor in the clip's wire-size. These things must make a difference somewhere.. Is it "splitting hairs" to be concerned about the proper fitting of a valve that literally "buzzes" during operation?.. or could reed-fit be the difference between an engine that starts quickly and stays running from drawing it's fuel mixture right away.. vs. the engine that requires several "exhaust-prime runs".. before the reed starts to do it's job?
EDIT: I would imagine that the successes experienced with using a pressure-bladder fuel-feed are directly related with reed-function.. because the reed now only has to draw air. The fuel is already present.. as well as constant.
EDIT: I would imagine that the successes experienced with using a pressure-bladder fuel-feed are directly related with reed-function.. because the reed now only has to draw air. The fuel is already present.. as well as constant.
Reeds
HI Roger,
You ask some very interesting questions! Most of which I unfortunately don't have any answers to.
I would add that it is "Attention to Detail" that separates the fast engines from the slow runners. As I have published previously, I was astonished to find that a 1000 RPM drop in a microscopically damaged reed. Damage I assume caused by dirt/sand ingestion. Perhaps one of our Australian readers can send a photo of the Australian designed reed which was a few hundred RPM faster than normal, but had a very short lifespan (at least with the one example I had). Certainly somebody put some thought into it's unique design...
Just when you think a reed retainer was just a reed retainer...you find out the thickness varies. I didn't know that, & don't know if it's important or not. Yet another variable I'll have to worry about! Perhaps smarter people than I will chime in with their thoughts. Great discussion though!
Cheers, Paul
You ask some very interesting questions! Most of which I unfortunately don't have any answers to.
I would add that it is "Attention to Detail" that separates the fast engines from the slow runners. As I have published previously, I was astonished to find that a 1000 RPM drop in a microscopically damaged reed. Damage I assume caused by dirt/sand ingestion. Perhaps one of our Australian readers can send a photo of the Australian designed reed which was a few hundred RPM faster than normal, but had a very short lifespan (at least with the one example I had). Certainly somebody put some thought into it's unique design...
Just when you think a reed retainer was just a reed retainer...you find out the thickness varies. I didn't know that, & don't know if it's important or not. Yet another variable I'll have to worry about! Perhaps smarter people than I will chime in with their thoughts. Great discussion though!
Cheers, Paul
Paulgibeault- Gold Member
- Posts : 259
Join date : 2011-09-24
Location : Leduc, Alberta Canada
Re: Reed clearance/gap
Thanks Paul, It's always good to have some feedback. It "is" an interesting subject. What shape was that reed that the Australian modeler had?
Here's an odd reed that I removed from an engine many years ago. It's approx. .004" thick.. and looks like it may be Stainless Steel. It's in pretty bad shape.. and I can't remember ever running it.

Here's an odd reed that I removed from an engine many years ago. It's approx. .004" thick.. and looks like it may be Stainless Steel. It's in pretty bad shape.. and I can't remember ever running it.


» What's the Best Reed for Cox Reed Valve Engines.
» Fastest reedy??
» Which reed is best???
» Reed me.........Please
» Reed Valves For .049
» Fastest reedy??
» Which reed is best???
» Reed me.........Please
» Reed Valves For .049
Page 1 of 1
Permissions in this forum:
You cannot reply to topics in this forum