Log in
Search
Latest topics
» WILLY NILLYby akjgardner Today at 7:55 pm
» Wen Mac Aeromite/Challenger
by rsv1cox Today at 6:45 pm
» Modelsmodels
by roddie Today at 6:07 pm
» Stick built rubber powered Scientific ME-109
by TD ABUSER Today at 4:07 pm
» Ignition Points for Ohlsson 23
by crankbndr Today at 2:29 pm
» 010 head stops glowing
by Cox International Today at 11:00 am
» Needle-Valve extensions (yellow) for Killer Bee
by Cox International Yesterday at 10:35 pm
» Unique Foxie partzie. Potential fishing line/paper weight or something else.
by rsv1cox Yesterday at 2:48 pm
» Cox P-40 Clone Project - I just can’t leave well enough alone.
by akjgardner Yesterday at 10:32 am
» COX .020 RC PROJECT
by TD ABUSER Yesterday at 9:29 am
» Roddie-Rigger.. a 2005 original design
by roddie Tue Sep 17, 2024 6:51 pm
» some pics....
by roddie Tue Sep 17, 2024 6:21 pm
Cox Engine of The Month
Micro 12VDC Generator with a Cox .049 Sure Start Diesel Engine
Page 7 of 31
Page 7 of 31 • 1 ... 6, 7, 8 ... 19 ... 31
Re: Micro 12VDC Generator with a Cox .049 Sure Start Diesel Engine
Where is the vid with a meter showing power out in volts and load tests.

1/2A Nut- Top Poster
- Posts : 3464
Join date : 2013-10-20
Age : 61
Location : Brad in Texas
Successful Start with a Muffler
This is appended to the thesis : http://www.steven-stanley-bayes.com/Cox%20.049%20SureStart%20Diesel.doc
Took 5 hours to figure out what the start up settings are. Cannot do these things. Want to prevent the spring and keep the engine nice and tidy. As much as I want to post the video of the engine with the muffler and add known background sounds for you all to hear how quiet the engine is, I will leave this to financially more advanced people.
Here is what I have found out ( all numbers approximate, fuel not accurately measured : added during attempts on many occasions ; fuel amount : less than 20mL and around 15mL in total ).
Started the engine with a Muffler. Very difficult.
Fuel : Began with standard Cox fuel of 39% Ether, 34% Kerosene, 24% Castor Oil, 3% Cetane Booster. Added more Cesare Booster thereafter to sustain the starts. As I experimented, I changed the fuel. I don't remember but I think I have started the engine with an increased Ether to Kerosene ratio : 49% Ether, 28% Kerosene, 20% Castor Oil, 3% Cetane Booster.
I have then again started the engine ( not from hot, but from near room temperature ) with 35%, Ether, 26% Kerosene, 26% Castor Oil, 13% Cetone Booster.
The standard fuel did not work at the beginning but may work. More tests are needed. The amount of Cetane Booster may be increased to 6%. Lower percentage may be OK but may require a faster reaction on the controls after start up to allow the engine to continue.
I, therefore, suggest to anyone who wants to start the engine with the standard Cox muffler to FIRST try this fuel ( and then do whatever one wants ) : 25% Castor Oil, 10% Cetane Booster, 25% Kerosene, 40% Ether.
Settings :
Compression : almost maximum BUT NEVER maximum. Just slightly before the maximum. Started also with the compression screw one sixteenth to one eighth turns open but had to increase slightly to sustain. Full compression does not start well but may and does not sustain well but may. Not very sure yet.
Air Valve ( Throttle ) and Fuel Needle Valve : Adjust Air Valve to fully open and Fuel Needle Valve to 5 OR Air Valve to half and Fuel Needle Valve to 4. Do 4 spring starts to get fuel in the lines. Then Air Valve to three quarters open, Fuel Needle Valve to three and three quarters turns open. Do 4 Spring Starts. Then Air Valve to half open and Fuel Needle Valve to three and a half turns open. Do 4 spring starts. May start but may not sustain. Keep Air Valve to half open. Adjust the Fuel Needle Valve to three and a quarter. Do 4 spring starts or more. Must start. Try also Fuel Needle Valve to three and three eighth turns open. Increase the compression just a touch, almost impossible to see. RPM must INCREASE. In case they increase and decrease, the compression screw has been tighten too much.
Therefore, with a Muffler, the settings are pretty much similar to these without. JUST A TOUCH HIGHER because of impeded fluid movement as expected. Thus : Air Valve : HALF OPEN ; Fuel Needle Valve THREE AND A QUARTER TO THREE AND A HALF TURNS OPEN ; COMPRESSION : AROUND ONE SIXTEENTH TURNS FROM FULL ( ONE EIGHTH TO FULL ) ; PREPAREDNESS : TO REACT ON THE COMPRESSION SCREW TOWARDS MORE CLOSED IN ORDER TO SUSTAIN ( JUST A SLIGHT TOUCH MORE CLOSED ).
Fuel can be initially pumped in by fully closing of the Air Valve ( finger on top without touching the Fuel Needle Valve ) and one or two spring starts. Do not flood.
Performance : extremely quiet. Quieter than a fly near the ear. Lower RPM increase as expected. Power, obviously, must decrease. The muffler hole can be enlarged for power noise compromise.
Messy : Yes. Spits Castor Oil through the muffler hole and then the aeration from the propeller blows the exhaust fluids backwards. Can be fixed simply : enlarge the muffler hole to what one wants as a power and noise compromise ( slightly larger for the nipple with the desired radius to be inserted ). Weld or solder a nipple with the desired radius to the hole. Connect a Copper pipe to the nipple and best solder. Connect a conical funnel like component to the pipe. Attach a circular plate to the conical shape in a way as to close the pipe BUT use a spacers to position this circular plate far from the conical pipe. From a kitchen sponge, cut a circular shape sponge with the same radius as the circular plate. Screw this to the circular plate. Ensure plenty of room between the conical exhaust and the sponge unless you want to muffle ( be aware you may burn the sponge in case too close ). The sponge will catch the exhaust Castor Oil.
This is an amazing engine!
Took 5 hours to figure out what the start up settings are. Cannot do these things. Want to prevent the spring and keep the engine nice and tidy. As much as I want to post the video of the engine with the muffler and add known background sounds for you all to hear how quiet the engine is, I will leave this to financially more advanced people.
Here is what I have found out ( all numbers approximate, fuel not accurately measured : added during attempts on many occasions ; fuel amount : less than 20mL and around 15mL in total ).
Started the engine with a Muffler. Very difficult.
Fuel : Began with standard Cox fuel of 39% Ether, 34% Kerosene, 24% Castor Oil, 3% Cetane Booster. Added more Cesare Booster thereafter to sustain the starts. As I experimented, I changed the fuel. I don't remember but I think I have started the engine with an increased Ether to Kerosene ratio : 49% Ether, 28% Kerosene, 20% Castor Oil, 3% Cetane Booster.
I have then again started the engine ( not from hot, but from near room temperature ) with 35%, Ether, 26% Kerosene, 26% Castor Oil, 13% Cetone Booster.
The standard fuel did not work at the beginning but may work. More tests are needed. The amount of Cetane Booster may be increased to 6%. Lower percentage may be OK but may require a faster reaction on the controls after start up to allow the engine to continue.
I, therefore, suggest to anyone who wants to start the engine with the standard Cox muffler to FIRST try this fuel ( and then do whatever one wants ) : 25% Castor Oil, 10% Cetane Booster, 25% Kerosene, 40% Ether.
Settings :
Compression : almost maximum BUT NEVER maximum. Just slightly before the maximum. Started also with the compression screw one sixteenth to one eighth turns open but had to increase slightly to sustain. Full compression does not start well but may and does not sustain well but may. Not very sure yet.
Air Valve ( Throttle ) and Fuel Needle Valve : Adjust Air Valve to fully open and Fuel Needle Valve to 5 OR Air Valve to half and Fuel Needle Valve to 4. Do 4 spring starts to get fuel in the lines. Then Air Valve to three quarters open, Fuel Needle Valve to three and three quarters turns open. Do 4 Spring Starts. Then Air Valve to half open and Fuel Needle Valve to three and a half turns open. Do 4 spring starts. May start but may not sustain. Keep Air Valve to half open. Adjust the Fuel Needle Valve to three and a quarter. Do 4 spring starts or more. Must start. Try also Fuel Needle Valve to three and three eighth turns open. Increase the compression just a touch, almost impossible to see. RPM must INCREASE. In case they increase and decrease, the compression screw has been tighten too much.
Therefore, with a Muffler, the settings are pretty much similar to these without. JUST A TOUCH HIGHER because of impeded fluid movement as expected. Thus : Air Valve : HALF OPEN ; Fuel Needle Valve THREE AND A QUARTER TO THREE AND A HALF TURNS OPEN ; COMPRESSION : AROUND ONE SIXTEENTH TURNS FROM FULL ( ONE EIGHTH TO FULL ) ; PREPAREDNESS : TO REACT ON THE COMPRESSION SCREW TOWARDS MORE CLOSED IN ORDER TO SUSTAIN ( JUST A SLIGHT TOUCH MORE CLOSED ).
Fuel can be initially pumped in by fully closing of the Air Valve ( finger on top without touching the Fuel Needle Valve ) and one or two spring starts. Do not flood.
Performance : extremely quiet. Quieter than a fly near the ear. Lower RPM increase as expected. Power, obviously, must decrease. The muffler hole can be enlarged for power noise compromise.
Messy : Yes. Spits Castor Oil through the muffler hole and then the aeration from the propeller blows the exhaust fluids backwards. Can be fixed simply : enlarge the muffler hole to what one wants as a power and noise compromise ( slightly larger for the nipple with the desired radius to be inserted ). Weld or solder a nipple with the desired radius to the hole. Connect a Copper pipe to the nipple and best solder. Connect a conical funnel like component to the pipe. Attach a circular plate to the conical shape in a way as to close the pipe BUT use a spacers to position this circular plate far from the conical pipe. From a kitchen sponge, cut a circular shape sponge with the same radius as the circular plate. Screw this to the circular plate. Ensure plenty of room between the conical exhaust and the sponge unless you want to muffle ( be aware you may burn the sponge in case too close ). The sponge will catch the exhaust Castor Oil.
This is an amazing engine!
Re: Micro 12VDC Generator with a Cox .049 Sure Start Diesel Engine
RknRusty wrote:If you're trying to crank any new engine with a muffler, you're making it much more difficult. Learn to crank, and break it in without a muffler. This lets you prime it at the exhaust port. Then when you get the hang of it, and the engine has settled in and will run dependably, you can install the muffler and re-learn how it needs to be primed and cranked. In a glow engine, if it starts brightly and stops in a few seconds, then it's needle is probably set too lean. Open 1/4 turn, re-prime and try again. Otherwise, it's possible there is a fuel feed problem.
Make sure the internal pickup of the tank is on the same horizontal plane as the venturi(not lower) so it doesn't fight gravity and drain back before its vacuum can pull it through the line. And if it's higher than the venturi it can flood the engine, though reed engines aren't quite as bad as rotary valve engines about that, but it can happen. Also it's important to use the shortest possible fuel line from the tank to the engine. After fixing any of the tank position problems, if all it will do is scream BRRAAAP and quit after burning off the prime, something could be clogging the Needle valve..
Rusty
Thanks a lot. Very true. a quarter turn more of fuel and air is what I have found out the hard way! To decrease the effect of start and stop, I slightly increase the compression and quickly " give more gas ( in this case air ) " by pushing the fishing cord which action quickly opens the air intake valve ( throttle ) and, after a while when the engine gets slightly more heated up I adjust the air valve ( throttle ) with the guitar tuning machine.
THANK YOU FOR THIS REPLY. INCREDIBLY HELPFUL. 100% TRIED, TESTED AND TRUE!
Re: Micro 12VDC Generator with a Cox .049 Sure Start Diesel Engine
1/2A Nut wrote:Where is the vid with a meter showing power out in volts and load tests.![]()
You sound like a manger of an R&D department. I also need breaks as well as to watch Mayday, UFO Declassified and Close Encounters. : )
The ONLY thing I have assembled so far is the Cox engine, the Cox tank and the " linkage " ( the guitar tuning machine, fishing cord, fishing hook and spring from Home Depot ). I have only been running the engine. What sounds like a few second job took a couple of months.
In order to be able to work easier, I have built a wooden stand.
Now here is the answer of your question :
The gray painted Aluminium support to which the engine is mounted is one half of the hole Aluminium enclosure. The other half slides into the first and there are screws to attach the two half all over the place. Because the first half of the enclosure is secured on the wooden pedestal, I will not be able to screw all screws in to support the assembly of the two halves of the enclosure : I will only use half of the screws which go on top of what you see on the picture.
On the second half of the enclosure, I will drill large holes to accommodate the old school analogue electro mechanical panel mount ampermeter and voltmeter as well as the switch.
The dynamo is to be on the front. The 1L tank : on top, connected to the Cox tank via an external needle valve.
The electrical connection is : Dynamo. From the positive, a wire to a fast diode. I prefer to loose 0.65 to 1V ( nasty ) but to protect the dynamo from current from the load. Then a 5mm fuse in a panel mount fuse housing. Then the switch. Then the ampermeter. Then the voltmeter. The ampermeter would show the leakage through the voltmeter and the load current. Nasty. However, I prefer to provide the user with the exact voltage across the load ( 2.5% accuracy ) then the exact current. Then a female cigarette lighter socket.
In case I install the blowers, they can be put either before the switch or before the ampermeter. In case they are before the switch, the blower will always blow when the alternator is spinning and giving between 3V and 24V consuming maximum 0.72W per blower. Otherwise, the blowers will not be always on but only after the user flips the switch to " on ".
Again : I have only these problems with things non related to the engine :
Lining up the pulley of the engine with the pulley of the dynamo.
Selecting the pulley gear ratio.
Finding elastic tape and trying to run the alternator without too much of a force by the belt because the more the belt pull the higher the wear on the crankcase axel housing ( the housing of the threaded axel where the propeller screws in ).
Assembling the dynamo, so the position of the dynamo can be readjusted to cover for belt stretching ( not sure whether can easily do so ) or using an " empty " wheel with a spring to pull the belt.
To avoid the wear of the crankcase axel housing, people line up their generators with their engines to provide a straight connection from the crankshaft to the rotor. I prefer to allow users to change pulley gear ratio as they please with just changing one or two pulleys.
I have an idea of how to decrease the wear of the crankcase axel housing : I do not know whether I can do but a company can easily manufacture a wheel with a rubber tire. The " tire " goes inside the pulley canal ( just like the belt ) where there is no belt. This wheel is " empty " and does not rotate anything. The only thing this wheel does is counters the pull of the belt which pulls the spinning crankshaft axel in the direction towards the dynamo. The empty wheel position and counter tension can be made adjustable by moving the wheel towards the engine pulley or away before securing the wheel with a screw or nut, just like a car alternator. Also, the wheel tension can be defined by a spring which moves the wheel towards the engine pulley. The strength of the string can be selected. The wheel can be mount on a movable arm, controlled by the spring.
For now, I will not do so.
Video : Cox 1
www.youtube.com/watch?v=Y7FfparKL78&list=UUiFdItymm78mcEB5Qlu67tg
Cox .049 Surestart Diesel Engine : Break In
Engine : Cox .049 SureStart Diesel Engine
Muffler : Not Installed for this video
Fuel : 38% Ether ( John Deere 80 Starter Fluid ), 33% Kerosene ( Clear ), 23% Castor Oil, 3% Cetone Booster ( 2 EthylExyl Nitrate & Xylene )
Amount of Fuel : 10mL
Start Up Settings :
Air Valve ( Throttle ) : one quarter open
Fuel Needle Valve : three and a quarter turns open
Compression : one eighth turn open
Total Run : 8 minutes
ALL NUMBERS APPROXIMATE.
Comments :
Engine initially primed with 0.5mL fuel.
Preparation for start : Air Valve ( Throttle ) fully open. Compression : one eighth turn open. Fuel Needle Valve : 5 turns open. A few spring starts to bring fuel in. Then Fuel Needle Valve : 4 turns open. A few spring starts. Then wait for 30 seconds for the fuel to settle in the crankcase. Then Fuel Needle Valve : three and a quarter turns open. A few spring starts. Then Air Valve : three quarters open. A few spring starts. Then Air Valve : half open. A few spring starts. Then Air Valve : one quarter open. A few spring starts.
The engine should start with Fuel Needle Valve three and quarter turns open, Compression Screw one eighth open and Air Valve ( Throttle ) one quarter through half open.
Reason for engine stop after running ( last minutes of the video ) : Not enough fuel in the tank. Only a tiny amount. Even when the Air Valve ( Throttle ) was fully closed with a finger and at low compression, the engine would not suck in fuel but only air ( from the fuel tank ) because of the lack of sufficient amount of fuel in the fuel tank.
Hammer : A standard hammer is lifted to nearly 90 degrees while self supported on the floor and released on a wooden plank ( approximately half an inch thick ) to make a reference noise for evaluation of the engine noise.
Video and Audio : Picture not synchronised with sound but very close.
Cox .049 Surestart Diesel Engine : Break In
Engine : Cox .049 SureStart Diesel Engine
Muffler : Not Installed for this video
Fuel : 38% Ether ( John Deere 80 Starter Fluid ), 33% Kerosene ( Clear ), 23% Castor Oil, 3% Cetone Booster ( 2 EthylExyl Nitrate & Xylene )
Amount of Fuel : 10mL
Start Up Settings :
Air Valve ( Throttle ) : one quarter open
Fuel Needle Valve : three and a quarter turns open
Compression : one eighth turn open
Total Run : 8 minutes
ALL NUMBERS APPROXIMATE.
Comments :
Engine initially primed with 0.5mL fuel.
Preparation for start : Air Valve ( Throttle ) fully open. Compression : one eighth turn open. Fuel Needle Valve : 5 turns open. A few spring starts to bring fuel in. Then Fuel Needle Valve : 4 turns open. A few spring starts. Then wait for 30 seconds for the fuel to settle in the crankcase. Then Fuel Needle Valve : three and a quarter turns open. A few spring starts. Then Air Valve : three quarters open. A few spring starts. Then Air Valve : half open. A few spring starts. Then Air Valve : one quarter open. A few spring starts.
The engine should start with Fuel Needle Valve three and quarter turns open, Compression Screw one eighth open and Air Valve ( Throttle ) one quarter through half open.
Reason for engine stop after running ( last minutes of the video ) : Not enough fuel in the tank. Only a tiny amount. Even when the Air Valve ( Throttle ) was fully closed with a finger and at low compression, the engine would not suck in fuel but only air ( from the fuel tank ) because of the lack of sufficient amount of fuel in the fuel tank.
Hammer : A standard hammer is lifted to nearly 90 degrees while self supported on the floor and released on a wooden plank ( approximately half an inch thick ) to make a reference noise for evaluation of the engine noise.
Video and Audio : Picture not synchronised with sound but very close.
Re: Micro 12VDC Generator with a Cox .049 Sure Start Diesel Engine
Ah, bleeding knuckles, dripping with castor oil, smelly, noisey, cranky engines, trying to source fuel components, welcome to our world

Oldenginerod- Top Poster
- Posts : 4006
Join date : 2012-06-15
Age : 61
Location : Drouin, Victoria
Re: Micro 12VDC Generator with a Cox .049 Sure Start Diesel Engine
Oldenginerod wrote:Ah, bleeding knuckles, dripping with castor oil, smelly, noisey, cranky engines, trying to source fuel components, welcome to our world![]()
Thanks. The bleeding was because of stupidity to put a hand on the propeller's way and because I got used to a 3.5 inch propeller where controls are easily accessible from the front too. I may revert to the 3.5 inch propeller because the eight inch takes a lot of room. I wish I can have a 3.5 inch propeller with many blades. I was thinking of putting two 3.5 inch propellers next to each other to make a six blade propeller.
I also have a few 2 inch fans with many blades which I may use on the dynamo. I may have a look at whether they may provide enough aeration for the engine and use them.
All these fuel components are easy to get. Ether and Castor Oil are very expensive here.
The noise is not as bad and is comparable with other of the shelf generators and grass trimmers, loan mowers, mini bikes, etcetera and even much quieter than these.
I understand your sense of humour and this is not the message to respond with this but the noise and the leaking Castor Oil have become big issues here. Thus, the standard Cox muffler with any size of hole and a nipple and a pipe can reduce the noise and throw the Castor Oil away from the user and the generator. Because the generator has to be accessible from the front and the back, a good idea would be to pint the pipe to throw Castor Oil to the side and down.
Also, the exhaust Castor Oil can be caught or channeled by a sponge positioned near this pipe.
Correction on the Muffler
I wrote hare the muffler was not symmetrically positioned in respect to the exhaust holes.
I made a mistake.
I filed one of the sides of the Cox muffler and installed the muffler in such a way as to point towards the front and to the right ( looking from the pilot's seat ). This way, the hole of the muffler is symmetrically positioned between the two sets of two exhaust lines per set. Thus, the fluids coming from the two sets of holes see the same resistance on the path of the exhaust fluids ( gases and Castor Oil and, hopefully not much, unburned fuel ).
Although this may increase the overall resistance, I have decided to introduce this symmetry. I have not started the engine with the muffler installed as per Cox requirements where the position of the muffler hole is not between the two sets of exhaust lines but is across one of them.
Still, the engine started and worked extremely quietly, incomparable to the noise of the non muffled engine which you can all hear in the video.
Also, I think, but I am not sure, the low RPM noise is similar to the high RPM noise but this may be wrong, probably, because the low RPM noise is more irritating.
I made a mistake.
I filed one of the sides of the Cox muffler and installed the muffler in such a way as to point towards the front and to the right ( looking from the pilot's seat ). This way, the hole of the muffler is symmetrically positioned between the two sets of two exhaust lines per set. Thus, the fluids coming from the two sets of holes see the same resistance on the path of the exhaust fluids ( gases and Castor Oil and, hopefully not much, unburned fuel ).
Although this may increase the overall resistance, I have decided to introduce this symmetry. I have not started the engine with the muffler installed as per Cox requirements where the position of the muffler hole is not between the two sets of exhaust lines but is across one of them.
Still, the engine started and worked extremely quietly, incomparable to the noise of the non muffled engine which you can all hear in the video.
Also, I think, but I am not sure, the low RPM noise is similar to the high RPM noise but this may be wrong, probably, because the low RPM noise is more irritating.
Re: Micro 12VDC Generator with a Cox .049 Sure Start Diesel Engine
StevenStanleyBayes wrote:www.youtube.com/watch?v=Y7FfparKL78&list=UUiFdItymm78mcEB5Qlu67tg
Cox .049 Surestart Diesel Engine : Break In
Engine : Cox .049 SureStart Diesel Engine
Muffler : Not Installed for this video
Fuel : 38% Ether ( John Deere 80 Starter Fluid ), 33% Kerosene ( Clear ), 23% Castor Oil, 3% Cetone Booster ( 2 EthylExyl Nitrate & Xylene )
Amount of Fuel : 10mL
Start Up Settings :
Air Valve ( Throttle ) : one quarter open
Fuel Needle Valve : three and a quarter turns open
Compression : one eighth turn open
Total Run : 8 minutes
ALL NUMBERS APPROXIMATE.
Comments :
Engine initially primed with 0.5mL fuel.
Preparation for start : Air Valve ( Throttle ) fully open. Compression : one eighth turn open. Fuel Needle Valve : 5 turns open. A few spring starts to bring fuel in. Then Fuel Needle Valve : 4 turns open. A few spring starts. Then wait for 30 seconds for the fuel to settle in the crankcase. Then Fuel Needle Valve : three and a quarter turns open. A few spring starts. Then Air Valve : three quarters open. A few spring starts. Then Air Valve : half open. A few spring starts. Then Air Valve : one quarter open. A few spring starts.
The engine should start with Fuel Needle Valve three and quarter turns open, Compression Screw one eighth open and Air Valve ( Throttle ) one quarter through half open.
Reason for engine stop after running ( last minutes of the video ) : Not enough fuel in the tank. Only a tiny amount. Even when the Air Valve ( Throttle ) was fully closed with a finger and at low compression, the engine would not suck in fuel but only air ( from the fuel tank ) because of the lack of sufficient amount of fuel in the fuel tank.
Hammer : A standard hammer is lifted to nearly 90 degrees while self supported on the floor and released on a wooden plank ( approximately half an inch thick ) to make a reference noise for evaluation of the engine noise.
Video and Audio : Picture not synchronised with sound but very close.
USUALLY THE ENGINE STARTS MUCH MORE EASILY with only a four spring starts at the start up settings. I think, other than with the muffler, this was the most difficult start I had had since I found the start up algorithm.
Re: Micro 12VDC Generator with a Cox .049 Sure Start Diesel Engine
Hey Steve, it sure is good to see it running. Rod's funny too isn't he Lol.
Okay, got grits on the burner so I could only watch up to 11:48. I'd like to make some suggestions.
First, it may not be a problem, but shorten your fuel line as much as possible without kinking it. Especially the big bottom loop so it's not fighting gravity.
Next is from start to stop I see you being too aggressive with the machine. Starting with the windup, it looked like you were wrapping it 1-1/2 or 2 turns. You may find better results with one turn. On some glow engines that are being especially contrary, I have found many times that 1/2 turn gets results when more won't do anything to ignite a charge.
The next thing I saw is your adjustments are very rapid. "Tweaking" means really considered and methodical. Once you get it running, make small adjustments and wait for it to adapt to your change in mixture, air, or compression. Temperature changes slowly compared to your twisting on the F/A mix, and it's just as much of a component as fuel, compression, and air. So you have to wait for it all to catch up.
I'm guessing that's the air valve to the intake on the long snorkel I see coming out of the top? Everyone has to learn these things when first getting the hang of it, and no two engines will act the same, so it's hard, but breath deep, make calm moves and you and it become a team. And get a box of Snoopy bandaids like I have near my table all the time.
Rusty
EDIT: I'be been writing this for an hour while I cook supper, and I see other replies. If I'm contradictory or redundant anywhere, I'll get back to it later.
Time for chow!
Rusty
Double Edit: Nevermind, those were all your own replies.
Okay, got grits on the burner so I could only watch up to 11:48. I'd like to make some suggestions.
First, it may not be a problem, but shorten your fuel line as much as possible without kinking it. Especially the big bottom loop so it's not fighting gravity.
Next is from start to stop I see you being too aggressive with the machine. Starting with the windup, it looked like you were wrapping it 1-1/2 or 2 turns. You may find better results with one turn. On some glow engines that are being especially contrary, I have found many times that 1/2 turn gets results when more won't do anything to ignite a charge.
The next thing I saw is your adjustments are very rapid. "Tweaking" means really considered and methodical. Once you get it running, make small adjustments and wait for it to adapt to your change in mixture, air, or compression. Temperature changes slowly compared to your twisting on the F/A mix, and it's just as much of a component as fuel, compression, and air. So you have to wait for it all to catch up.
I'm guessing that's the air valve to the intake on the long snorkel I see coming out of the top? Everyone has to learn these things when first getting the hang of it, and no two engines will act the same, so it's hard, but breath deep, make calm moves and you and it become a team. And get a box of Snoopy bandaids like I have near my table all the time.
Rusty
EDIT: I'be been writing this for an hour while I cook supper, and I see other replies. If I'm contradictory or redundant anywhere, I'll get back to it later.
Time for chow!
Rusty
Double Edit: Nevermind, those were all your own replies.
_________________
Don't Panic!
...and never Ever think about how good you are at something...
while you're doing it!
My Hot Rock & Blues Playlist
...and never Ever think about how good you are at something...
while you're doing it!
My Hot Rock & Blues Playlist
RknRusty- Rest In Peace
- Posts : 10869
Join date : 2011-08-10
Age : 68
Location : South Carolina, USA
Re: Micro 12VDC Generator with a Cox .049 Sure Start Diesel Engine
Or a gear on the output shaft that turns another gear which has a pulley bolted to its face.StevenStanleyBayes wrote: Finding elastic tape and trying to run the alternator without too much of a force by the belt because the more the belt pull the higher the wear on the crankcase axel housing
I have an idea of how to decrease the wear of the crankcase axel housing : I do not know whether I can do but a company can easily manufacture a wheel with a rubber tire. The " tire " goes inside the pulley canal ( just like the belt ) where there is no belt. This wheel is " empty " and does not rotate anything. The only thing this wheel does is counters the pull of the belt which pulls the spinning crankshaft axel in the direction towards the dynamo. The empty wheel position and counter tension can be made adjustable by moving the wheel towards the engine pulley or away before securing the wheel with a screw or nut, just like a car alternator. Also, the wheel tension can be defined by a spring which moves the wheel towards the engine pulley. The strength of the string can be selected. The wheel can be mount on a movable arm, controlled by the spring.
Rusty
_________________
Don't Panic!
...and never Ever think about how good you are at something...
while you're doing it!
My Hot Rock & Blues Playlist
...and never Ever think about how good you are at something...
while you're doing it!
My Hot Rock & Blues Playlist
RknRusty- Rest In Peace
- Posts : 10869
Join date : 2011-08-10
Age : 68
Location : South Carolina, USA
Re: Micro 12VDC Generator with a Cox .049 Sure Start Diesel Engine
RknRusty wrote:Hey Steve, it sure is good to see it running. Rod's funny too isn't he Lol.
Okay, got grits on the burner so I could only watch up to 11:48. I'd like to make some suggestions.
First, it may not be a problem, but shorten your fuel line as much as possible without kinking it. Especially the big bottom loop so it's not fighting gravity.
Next is from start to stop I see you being too aggressive with the machine. Starting with the windup, it looked like you were wrapping it 1-1/2 or 2 turns. You may find better results with one turn. On some glow engines that are being especially contrary, I have found many times that 1/2 turn gets results when more won't do anything to ignite a charge.
The next thing I saw is your adjustments are very rapid. "Tweaking" means really considered and methodical. Once you get it running, make small adjustments and wait for it to adapt to your change in mixture, air, or compression. Temperature changes slowly compared to your twisting on the F/A mix, and it's just as much of a component as fuel, compression, and air. So you have to wait for it all to catch up.
I'm guessing that's the air valve to the intake on the long snorkel I see coming out of the top? Everyone has to learn these things when first getting the hang of it, and no two engines will act the same, so it's hard, but breath deep, make calm moves and you and it become a team. And get a box of Snoopy bandaids like I have near my table all the time.
Rusty
EDIT: I'be been writing this for an hour while I cook supper, and I see other replies. If I'm contradictory or redundant anywhere, I'll get back to it later.
Time for chow!
Rusty
Double Edit: Nevermind, those were all your own replies.
As usually, you are 100% right and everything you say is extremely useful! Thanks a lot for your replies and help.
I am sorry you are into Nitro and not diesel. I was to get much more help although others had helped a lot too. However, although diesel is more powerful, Nitro is the correct fuel for this project. This is because a rechargeable battery with the necessary circuit ( usually sold as a ready to use IC ) can do the job of starting up and be used longer. The most important feature of Nitro is customer friendliness. I saw videos on YouTube where people put the engine next to compression and then, with the battery on, just turn the " knob " on the propeller just slightly, say one eighth turn, and the engine start. Much easier than turning the key of a key start car ( I am not sure whether these are still manufactured as everything is with a button now ). And the engine is on, up and running. This is what customers want. However, I have already started with diesel and I will continue and, then, everyone can realise what the project would be with a Nitro engine. Besides, Nitro fuel is sold readily available in almost any country in the world whereas Davis Diesel is sold only in some countries and The UK is the only country in the world I have heard of where they sell all of the ingredients of a diesel fuel and very inexpensively.
I am happy to hear you suggest only one spring turn. Cox does too. I have never tried 1 turn but I must. The reason is I cannot even think of a possibility to start with 1 turn but I must as everyone says this is easier to start. I promise I would try as long as I do not forget.
You are 100% right on the length of the fuel line : must be as short as possible and, I think, shortening will definitely help. The reason to be so long is because I used the maximum allowed ( 10cm ) before I positioned the tank and I did not know where and how exactly to position the tank then, so I got 10cm fuel line with the idea to cut after and I did not. I must, though.
You are right with the rapid tweaking too. Must not be done and does not show anything because the engine must be able to reliably work with a given settings over a long period as the engine may perfectly OK work with some settings for a few seconds and then stop. I mixed only 10mL of fuel and wanted to run many scenarios to achieve low RPM just to see how low the engine can go. I think, the most reliable results were with Fuel Needle Valve to normal ( between 2.75 and 3.75 turns open and then I used the Air Valve ( throttle ) and Compression controls to leash the power of the engine.
The snorkel is for the Air Valve ( Throttle ). I keep forgetting which side to turn for what! : ) I know only, when I press on the fishing cord, I can give a lot of " gas " ( air in this case ) as quickly as I want.
Thanks for your reply. As far as the bad aids go, I think but I am not sure, Ether, Kerosene and Castor Oil work very well as an oxidant against bleeding! The bleeding stopped immediately after started. After the test, I just washed hands and : no bleeding! Do not use this as a method of stopping of bleeding! : )
I was so impatient to make the video, so I did not warm the fuel up and the fuel was at freezing temperatures thanks to the John Deere squeeze can with propellants. I think, this is one of the major reasons for the engine to start with such a difficulty.
Another thing : I have found this out : During start up, STOP AND WAIT for 30 seconds after the fuel is loaded in the crankcase to make the fuel settle down in the crankcase and then do a spring start so the fuel is shot up into the upper cylinder. I think this is very useful and I will post this as a separate reply topic.
During start up, STOP AND WAIT
I have found this out : During start up, STOP AND WAIT for 30 seconds AFTER the fuel is loaded in the crankcase to make the fuel settle down in the crankcase and then do a spring start so the fuel is shot up into the upper cylinder.
Ensure the amount of fuel is not as much as to flood the engine.
Ensure the amount of fuel is not as much as to flood the engine.
Re: Micro 12VDC Generator with a Cox .049 Sure Start Diesel Engine
RknRusty wrote:Or a gear on the output shaft that turns another gear which has a pulley bolted to its face.StevenStanleyBayes wrote: Finding elastic tape and trying to run the alternator without too much of a force by the belt because the more the belt pull the higher the wear on the crankcase axel housing
I have an idea of how to decrease the wear of the crankcase axel housing : I do not know whether I can do but a company can easily manufacture a wheel with a rubber tire. The " tire " goes inside the pulley canal ( just like the belt ) where there is no belt. This wheel is " empty " and does not rotate anything. The only thing this wheel does is counters the pull of the belt which pulls the spinning crankshaft axel in the direction towards the dynamo. The empty wheel position and counter tension can be made adjustable by moving the wheel towards the engine pulley or away before securing the wheel with a screw or nut, just like a car alternator. Also, the wheel tension can be defined by a spring which moves the wheel towards the engine pulley. The strength of the string can be selected. The wheel can be mount on a movable arm, controlled by the spring.
Rusty
THANK YOU FOR THIS EXCELLENT SUGGESTION!
Yes, gears will solve the problem. The best, there are dynamos and generators with built in gears. Usually, these are for 100RPM or around use but any gears can be put in a dynamo and a generator. Usually, they are sold sealed but I do not know what else they do. I can imagine there are some where the customer puts the gears and various gears are sold in the pack by the manufacturer. These are usually expensive.
Gears are sold separately but lining them up is very difficult in the out of a company environment. Also, when the gears break, finding them and replacing them is very difficult as opposed to changing the belt.
Yet, gears are better and can be better centered.
Other ways I have found are to center the propeller axel ( an extended one ) with two ball bearings. Requires immense accuracy.
To channel the belt with " empty " wheels in such a way, so the belt touches the engine pulley only on top and bottom with equal force. Teethed belt and pulleys are welcome. Again, not very easy to do in an out of a company environment.
Re: Micro 12VDC Generator with a Cox .049 Sure Start Diesel Engine
do it just like me
directly coupled
then there is almost no wear and the engine bearings will take a lot of the force
directly coupled
then there is almost no wear and the engine bearings will take a lot of the force
robot797- Platinum Member
- Posts : 766
Join date : 2013-07-28
Age : 34
Status Report
Started to make a bracket for the dynamo.
I use Aluminium for the bracket because Aluminium does not affect magnets and magnetic lines, i. e. Aluminium is non ferrous. I even have a scratch pad for the guitar made of Aluminium and the backplate made of Bronze ( also non ferrous ).
However, I do not have any screws except steel. Thus. I stopped and will continue after I go to the shop and get brass screws, nuts and washers.
The problem is : I cannot make a good 90 degree angle with hand tools. I don't even have a big vice. With a big vice or anvil and a hammer, better results can be achieved.
The best way to do this is with a torch or fire where Aluminium can be heated and bent to any shape. I do not have these and do not want to purchase these, although there are inexpensive, ready to use bottle torches where the gun is on the bottle and they are usually for single use although there may be some which are rechargeable.
Managed to make some angle, kind of 90 degrees. Can re twist when done for a fine adjustment.
Problem : the dynamo axel ( the rotor ) is very short thin and cylindrical. Cannot figure out very well how to attach the pulleys. Superglue may be best to be avoided. Extension difficult. Heat shrinks may or may not do.
I use Aluminium for the bracket because Aluminium does not affect magnets and magnetic lines, i. e. Aluminium is non ferrous. I even have a scratch pad for the guitar made of Aluminium and the backplate made of Bronze ( also non ferrous ).
However, I do not have any screws except steel. Thus. I stopped and will continue after I go to the shop and get brass screws, nuts and washers.
The problem is : I cannot make a good 90 degree angle with hand tools. I don't even have a big vice. With a big vice or anvil and a hammer, better results can be achieved.
The best way to do this is with a torch or fire where Aluminium can be heated and bent to any shape. I do not have these and do not want to purchase these, although there are inexpensive, ready to use bottle torches where the gun is on the bottle and they are usually for single use although there may be some which are rechargeable.
Managed to make some angle, kind of 90 degrees. Can re twist when done for a fine adjustment.
Problem : the dynamo axel ( the rotor ) is very short thin and cylindrical. Cannot figure out very well how to attach the pulleys. Superglue may be best to be avoided. Extension difficult. Heat shrinks may or may not do.
Re: Micro 12VDC Generator with a Cox .049 Sure Start Diesel Engine
robot797 wrote:do it just like me
directly coupled
then there is almost no wear and the engine bearings will take a lot of the force
THANK YOU FOR THIS EXCELLENT SUGGESTION TOO!
Yes. This is a good way. There are several posts which show a generator directly connected to the engine. These can be directly coupled as an extension or what they call " pan cake " generators as the coxgen project.
However, I want to be able to gear the generator to the engine and adjust the gears when needed. This is why I have decided to use pulleys and a belt. Also these are supposed to be easier in a non company environment.
I do NOT know neither the engines RPM to energy graphics nor the dynamo's RPM to output energy graphics as these are not available.
Here is the dynamo I have : http://m.ebay.ca/itm/301096305936?_mwBanner=1 I will post this in a different topic. Looks like, after the diode drop of 0.65V to 1V, I need 6500RPM to get 12V AT ZERO LOAD. At higher loads, the dynamo may need to go to 8000RPM or more.
I will make a separate post reply with the subject.
However, I have visually examined the wire of the dynamo. The wire is so thin, I doubt the generator can display more than 0.5A. Also, the dynamo heats up a lot, so a separate fan is welcome and, probably, blowers too. I do not think I can make blowers for the dynamo at for now but I may try to squeeze a tiny fan, either the one I have or I can make one from 1mm Aluminium.
I can also make a, say, 3.5 inch multiblade propeller for the engine from a few 1mm Aluminium double blade propellers but this may be for after I make the initial version of the project.
Sullivan and many Chinese companies make pancake generators and there are very many of them. They are plastic and thus must be light. However, Sullivan and the Chinese charge more for these than a brand new rebuilt ( they use an old housing only, everything else is brand new ) alternator for most any car and truck.
For the record : I love the directly coupled with or without internal to the generator gears, the pancakes, the gear wheel ones and all non belt designs. I cannot easily make this for the prototype. A company can, I do not think I can.
Last edited by StevenStanleyBayes on Wed Mar 04, 2015 5:17 pm; edited 2 times in total
The Dynamo, The Fan and a Possible Self Made Propeller
Here is the dynamo I have : http://m.ebay.ca/itm/301096305936?_mwBanner=1 I will post this in a different topic. Looks like, after the diode drop of 0.65V to 1V, I need 6500RPM to get 12V AT ZERO LOAD. At higher loads, the dynamo may need to go to 8000RPM or more.
I do NOT know neither the engines RPM to energy graphics nor the dynamo's RPM to output energy graphics as these are not available. I would use pulleys which are easy to re adjust.
However, I have visually examined the wire of the dynamo. The wire is so thin, I doubt the generator can display more than 0.5A. Also, the dynamo heats up a lot, so a separate fan is welcome and, probably, blowers too. I do not think I can make blowers for the dynamo at for now but I may try to squeeze a tiny fan, either the one I have or I can make one from 1mm Aluminium.
I can also make a, say, 3.5 inch multiblade propeller for the engine from a few 1mm Aluminium double blade propellers but this may be for after I make the initial version of the project.
I do NOT know neither the engines RPM to energy graphics nor the dynamo's RPM to output energy graphics as these are not available. I would use pulleys which are easy to re adjust.
However, I have visually examined the wire of the dynamo. The wire is so thin, I doubt the generator can display more than 0.5A. Also, the dynamo heats up a lot, so a separate fan is welcome and, probably, blowers too. I do not think I can make blowers for the dynamo at for now but I may try to squeeze a tiny fan, either the one I have or I can make one from 1mm Aluminium.
I can also make a, say, 3.5 inch multiblade propeller for the engine from a few 1mm Aluminium double blade propellers but this may be for after I make the initial version of the project.
Re: Micro 12VDC Generator with a Cox .049 Sure Start Diesel Engine
ANY copper alloy and aluminium is a recipe for electrolytic disaster. Copper will eat aluminium quite quickly.StevenStanleyBayes wrote:Started to make a bracket for the dynamo.
I use Aluminium for the bracket because Aluminium does not affect magnets and magnetic lines, i. e. Aluminium is non ferrous. I even have a scratch pad for the guitar made of Aluminium and the backplate made of Bronze ( also non ferrous ).
However, I do not have any screws except steel. Thus. I stopped and will continue after I go to the shop and get brass screws, nuts and washers.
The problem is : I cannot make a good 90 degree angle with hand tools. I don't even have a big vice. With a big vice or anvil and a hammer, better results can be achieved.
The best way to do this is with a torch or fire where Aluminium can be heated and bent to any shape. I do not have these and do not want to purchase these, although there are inexpensive, ready to use bottle torches where the gun is on the bottle and they are usually for single use although there may be some which are rechargeable.
Managed to make some angle, kind of 90 degrees. Can re twist when done for a fine adjustment.
Problem : the dynamo axel ( the rotor ) is very short thin and cylindrical. Cannot figure out very well how to attach the pulleys. Superglue may be best to be avoided. Extension difficult. Heat shrinks may or may not do.
dinsdale- Account Deactivated by Owner
- Posts : 317
Join date : 2012-02-22
Re: Micro 12VDC Generator with a Cox .049 Sure Start Diesel Engine
StevenStanleyBayes wrote:Here is the dynamo I have : http://m.ebay.ca/itm/301096305936?_mwBanner=1 I will post this in a different topic. Looks like, after the diode drop of 0.65V to 1V, I need 6500RPM to get 12V AT ZERO LOAD. At higher loads, the dynamo may need to go to 8000RPM or more.
That looks like a regular, brushed, electric motor to me. I guess you'll need a separate test rig to characterize its operation as a generator/dynamo.
Surfer_kris- Diamond Member
- Posts : 1909
Join date : 2010-11-20
Location : Sweden
Re: Micro 12VDC Generator with a Cox .049 Sure Start Diesel Engine
StevenStanleyBayes wrote:
I do NOT know neither the engines RPM to energy graphics nor the dynamo's RPM to output energy graphics as these are not available.
Here are some typical power curves for the Cox .049 engines. A Sure Start on glow fuel is probably close to the Babe Bee, while on diesel there might be a little more torque for any given rpm.
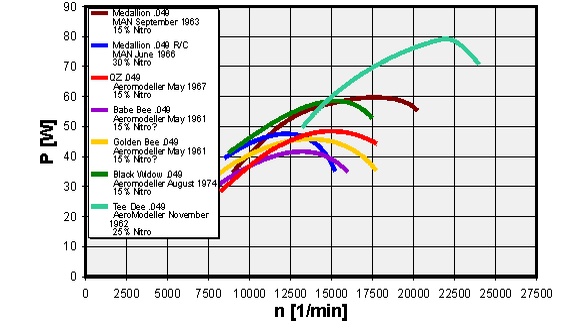
Surfer_kris- Diamond Member
- Posts : 1909
Join date : 2010-11-20
Location : Sweden
Re: Micro 12VDC Generator with a Cox .049 Sure Start Diesel Engine
dinsdale wrote:ANY copper alloy and aluminium is a recipe for electrolytic disaster. Copper will eat aluminium quite quickly.StevenStanleyBayes wrote:Started to make a bracket for the dynamo.
I use Aluminium for the bracket because Aluminium does not affect magnets and magnetic lines, i. e. Aluminium is non ferrous. I even have a scratch pad for the guitar made of Aluminium and the backplate made of Bronze ( also non ferrous ).
However, I do not have any screws except steel. Thus. I stopped and will continue after I go to the shop and get brass screws, nuts and washers.
The problem is : I cannot make a good 90 degree angle with hand tools. I don't even have a big vice. With a big vice or anvil and a hammer, better results can be achieved.
The best way to do this is with a torch or fire where Aluminium can be heated and bent to any shape. I do not have these and do not want to purchase these, although there are inexpensive, ready to use bottle torches where the gun is on the bottle and they are usually for single use although there may be some which are rechargeable.
Managed to make some angle, kind of 90 degrees. Can re twist when done for a fine adjustment.
Problem : the dynamo axel ( the rotor ) is very short thin and cylindrical. Cannot figure out very well how to attach the pulleys. Superglue may be best to be avoided. Extension difficult. Heat shrinks may or may not do.
I have heard Aluminium would prevent corrosion on iron and steel because of reversed potentials but I have never heard of an electrolytic disaster between Copper and Aluminium. So far, they seem to be OK and I have had other cases where I use Copper and Aluminium in electronics and electrical. After all, the best enclosures for electronics and electrical where there are a lot of touching Copper wires is Aluminium.
Regardless, I do take your point, however, I am pretty sure everything will be OK in the next few hundred years or for now.
Aluminium screws and nuts can be used on Aluminium for manufacturing purposes. For the prototype, most anything, except iron based products, such as steel, is OK. Please, note, ONLY iron is ferrous. Obviously, anything which contains iron, such as steel and other alloys is also ferrous to an extent which depends on the concentration of iron.
I agree with you, for production purposes, these things must be taken into account and Aluminium and Copper must not be mixed. I hope I remember this for the future.
Re: Micro 12VDC Generator with a Cox .049 Sure Start Diesel Engine
Surfer_kris wrote:StevenStanleyBayes wrote:Here is the dynamo I have : http://m.ebay.ca/itm/301096305936?_mwBanner=1 I will post this in a different topic. Looks like, after the diode drop of 0.65V to 1V, I need 6500RPM to get 12V AT ZERO LOAD. At higher loads, the dynamo may need to go to 8000RPM or more.
That looks like a regular, brushed, electric motor to me. I guess you'll need a separate test rig to characterize its operation as a generator/dynamo.
As I have been saying, this IS a simple brushed dynamo. Dynamo means a DC generator and not an AC one. Alternator means an AC generator and not a DC one.
There are brushes and there is NO information of the output. Some people say this can only give 16W, others say 100W. On the top of everything, there are a few version of RS555 with different characteristics and there are no markings to say which one I have. I accept this to be the most inexpensive one with the worst characteristics possible.
Thus, the safest way is to put a 0.5A fuse which will allow only 6W at 12V. 1A fuse may be OK and will give 12W at 12V. Some people claim this alternator can only display 1.3A at 12V others say more and some say more can only be achieved with a fan. Regardless of who says what a fan is always a good ide.
I will be happy to get 0.5A at 12V ( 6W ) for the first tests. I do not want to test the dynamo with an electric drill or the engine as I may damage the unknown generator when I put various of loads. All sources, however, show 0.6A at 12V to be safe.
For these who are interested, another, slightly more expensive purchase, is either YAF 54 ( already mentioned extensively ) or other Mabuchi motors ( RS555 is one of their motor generators ) or JOHNSON BRUSHED DYNAMOS. There is one which is 70W and is good for this project but I did not want to pay money for this. Sold by a US seller on eBay. Made in China. Johnson is a US company. I am not sure whether they design dynamos any more. Most likely these are old design which continues to be made in China or Johnson may have discontinued these and there are some old products around online still sold until available.
DYNAMOS AND ALTERNATORS ARE THE DUMBIEST ELECTRICAL DEVICES EVEN DUMBIER THAN A TRANSFORMER ( THERE ARE ACCURATE MEASUREMENT TRANSFORMERS WHICH ARE " ADVANCED " AS COMPARE TO THE OTHER ONES AND THE GENERATORS ) AND THERE MUST BE MANY OF THESE AVAILABLE ALL OVER THE PLACE FOR A DOLAR OR TWO. THERE IS NOTHING INSIDE TO PAY FOR.
The reality is there are not very many around and some of them have ridiculous prices. HENCE THE RS555.
You are welcome to use Johnson in case you so desire. Google search with " Johnson 70W DC Generator, eBay ". Or, here is the link : http://www.ebay.com/itm/280776426221?_trksid=p2060778.m1438.l2648&ssPageName=STRK%3AMEBIDX%3AIT
Re: Micro 12VDC Generator with a Cox .049 Sure Start Diesel Engine
Surfer_kris wrote:StevenStanleyBayes wrote:
I do NOT know neither the engines RPM to energy graphics nor the dynamo's RPM to output energy graphics as these are not available.
Here are some typical power curves for the Cox .049 engines. A Sure Start on glow fuel is probably close to the Babe Bee, while on diesel there might be a little more torque for any given rpm.
Thank you very much for this information. Any information is better than no information at all.
The only other information I have is the RPM range of Cox .049 SureStart Diesel Engine, which is 4000 to 13000 ( 12000 more likely ) RPM : http://coxengines.ca/cox-.049-rc-diesel-engine.html Scroll down and look to the right.
The other information I have is the maximal power of this engine is 40 to 50W, 50W is more cited.
Because diesel fuel is more powerful and as depends of the fuel component mixture ( which can be varied a lot ), I expect the engine to have a flatter power RPM response at RPM lower than the RPM where the maximal power is displayed. I expect but I am not sure the engine to reach maximal power at 6000 to 8000 RPM. I do not know, though. I expect the power output to decrease significantly after 9000 RPM. Again, I do not know.
Status Report
The attachment of the dynamo is almost ready. Have not purchased the brass screws yet.
May attach the dynamo to be able to work with 5 or 6 inch propellers. Intend to use the Cox 3.5 inch triple blade propeller which I expect to provide good aeration at low RPM. Can always be replaced. The dynamo can always be readjusted too.
An Aluminium angle bracket has been made on which a wooden bed is mounted to hold the dynamo and then an Aluminium top bracket with brass screws can be used to hold the dynamo stable.
The angle bracket will be screwed onto the enclosure with brass screws too. There will not be ferrous materials in close proximity to the dynamo.
May attach the dynamo to be able to work with 5 or 6 inch propellers. Intend to use the Cox 3.5 inch triple blade propeller which I expect to provide good aeration at low RPM. Can always be replaced. The dynamo can always be readjusted too.
An Aluminium angle bracket has been made on which a wooden bed is mounted to hold the dynamo and then an Aluminium top bracket with brass screws can be used to hold the dynamo stable.
The angle bracket will be screwed onto the enclosure with brass screws too. There will not be ferrous materials in close proximity to the dynamo.
Page 7 of 31 • 1 ... 6, 7, 8 ... 19 ... 31

» car engine diesel??? (aka generator V3)
» How to start a model diesel engine.......For Kim.
» RC Cars Cox 0.49 (Cox Stocker Kyosho f1,beetle) Killer Bee Backplate New Video!
» 5 Sure Start Engine Radial
» little generator
» How to start a model diesel engine.......For Kim.
» RC Cars Cox 0.49 (Cox Stocker Kyosho f1,beetle) Killer Bee Backplate New Video!
» 5 Sure Start Engine Radial
» little generator
Page 7 of 31
Permissions in this forum:
You cannot reply to topics in this forum